Advanced Incineration Technology
Vertical Combustor
For a Sustainable Future
Our Mission:
To make a better living environment on a global scale
Plantec Asia Pacific Pte Ltd was established as an international business development company based in Singapore. We aim to promote the Vertical Combustor - a new type of incineration technology invented in Japan - throughout the Asia Pacific region. As the issue of cost-effective and sustainable waste management system has become one of the biggest global challenges in recent years, Plantec Asia Pacific strongly believes that Vertical Combustor is the solution.
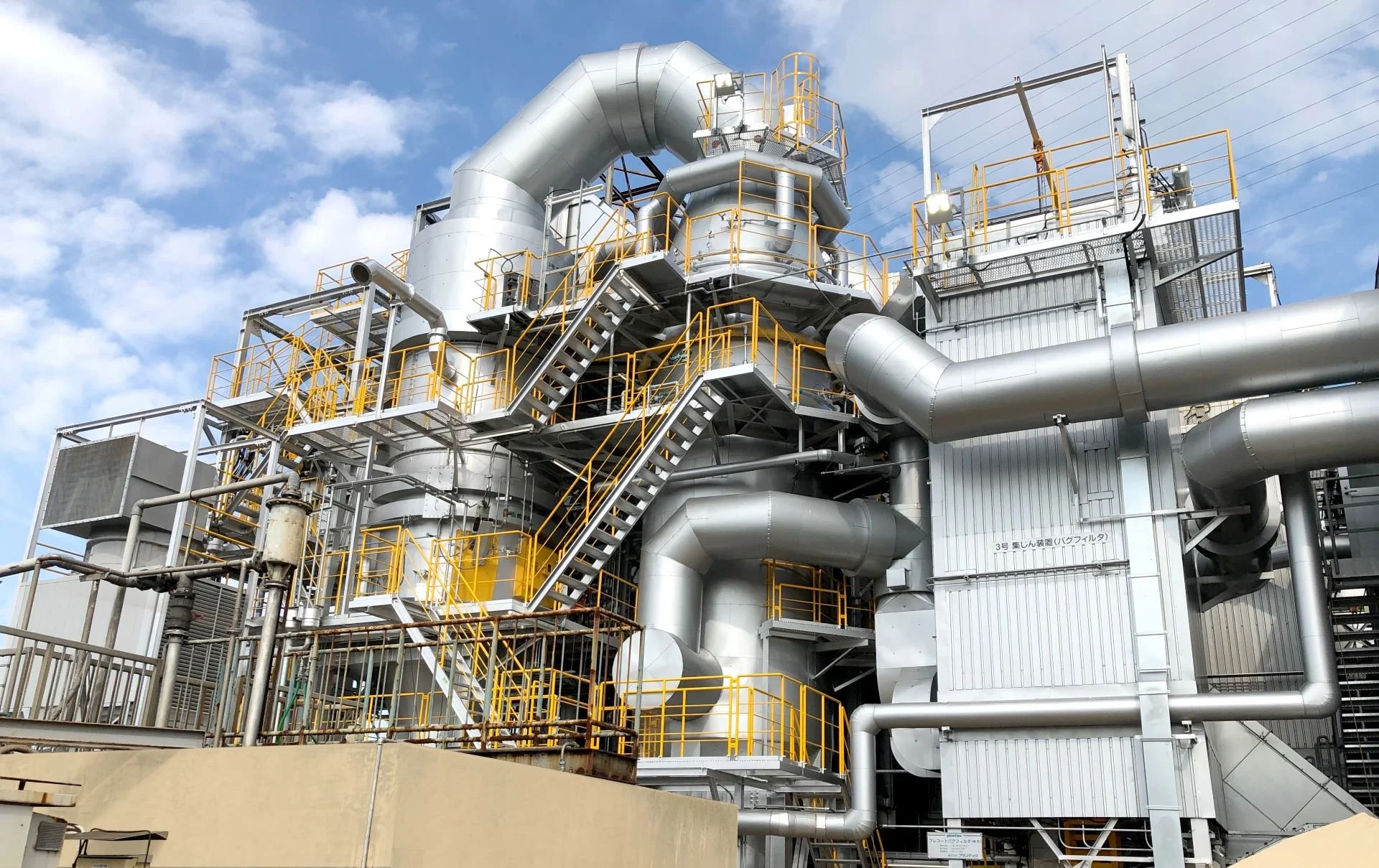
Vertical Combustor
Plantec's uniquely developed “Vertical Combustor” safely and efficiently processes a variety of waste materials. It also contributes to a sustainable society through thermal recycling solutions such as waste-to-energy.

Flue Gas Treatment
Plantec's uniquely developed dry chemical reaction dust collector, “Turbo Chemical Baghouse” reliably captures and removes all harmful substances, including dioxins and mercury.

170 Plants Worldwide
Our expertise is recognized not only in Japan but globally, contributing to the improvement of living environments in countries such as the United Arab Emirates (Dubai), Singapore, and Indonesia.
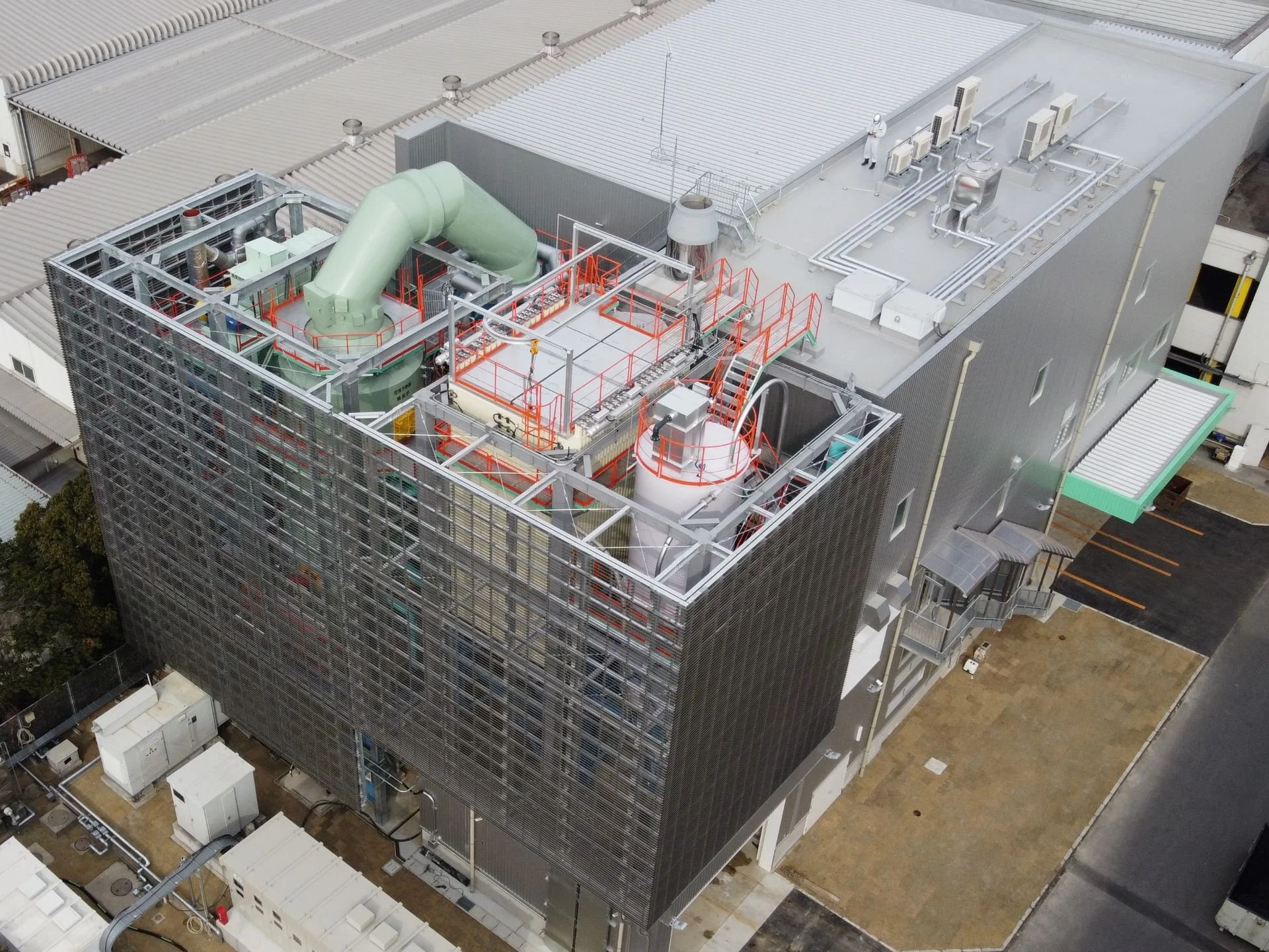
Let’s Work Together
We’re always looking for new opportunities and are comfortable working internationally. Please get in touch and one of our project managers will contact you about beginning the proposal process.
News & Events
Watch our videos
Movies above are excerpts from the TV programs broadcasted on BS Japan.
Contact us
We’re always looking for new opportunities and are comfortable working internationally.
Please get in touch and one of our project managers will contact you about beginning the proposal process.
Plantec Asia Pacific Pte Ltd
Phone: +65 6222 1114
Email: info@plantec-ap.com
Address: 380 Jalan Besar, #10-01 ARC 380, Singapore 209000
Office Hours: 9 am to 6 pm on Monday to Friday